Reciprocating vs Rotary Screw Air Compressors: An Overview
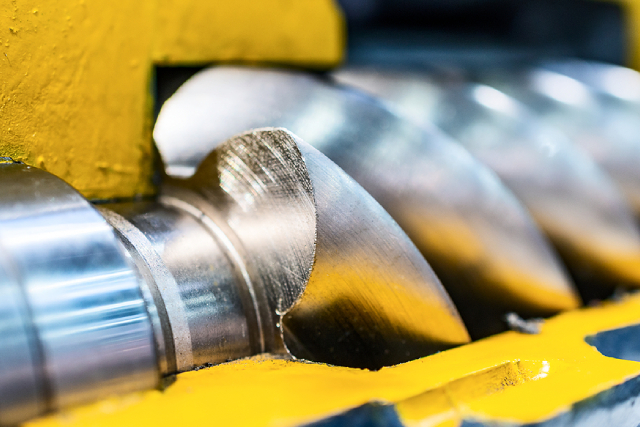
When buying an air compressor, many face the dilemma of selecting between a reciprocating and a rotary screw model. Though both perform the same core function, they differ in operation and suitability for specific applications. Factors like air output (CFM), usage frequency, cleanliness, maintenance, and efficiency play a key role in making a final decision. This article compares these two types of compressors and highlights the applications they best serve.
What Is a Reciprocating Air Compressor?
A reciprocating or piston-type air compressor consists of a cylinder, a piston, and a crankshaft. The piston moves back and forth within the cylinder, driven by the crankshaft, causing a motion that draws in air through an intake valve on the downward stroke and compresses it on the upward stroke, expelling the compressed air through a discharge valve.
Reciprocating compressors are available as single-stage or two-stage models. Single-stage compressors compress air in one stroke, while two-stage models compress it in two stages: first to an intermediate pressure, then to a higher pressure. The latter configuration typically provides a higher level of efficiency and output.
One of the key advantages of reciprocating air compressors is that they are ideal for intermittent use in applications requiring low air volume. Additionally, their simple, easy to maintain design means users can repair or replace parts themselves should the need arise. Commonly used in small workshops, auto repair centres, and other settings with modest CFM requirements, they are valued for their durability and versatility.
What Is a Rotary Screw Air Compressor?
A rotary screw compressor features two interlocking helical rotors inside a cylinder. As the rotors turn, air is drawn in through an inlet valve, becomes compressed as it moves through the grooves of the rotors, and is expelled through an outlet valve. Unlike its reciprocating counterpart, rotary screw compressors have fewer moving components, making them more durable and reliable and can last two to four times longer. And while they have a higher initial cost, their longevity and efficiency make them a worthwhile investment for many industrial users.
Because of their design, these compressors excel in continuous operation and high-airflow (CFM) applications. They provide steady, high-pressure output with minimal pulsation and energy loss. Additionally, their low vibration and noise levels make them ideal for industrial settings, such as production lines, conveyor systems, plastic moulding, woodworking, and more. Overall, by combining efficiency, reliability, and quiet operation, rotary screw compressors are the preferred choice for demanding, high-volume compressed air needs.
A Summary of the Key Differences Between Reciprocating and Rotary Screw Air Compressors
1. Maximum Delivery Pressure
A compressor’s maximum delivery pressure (PSI) is one of the key factors that needs to match your application's requirements. Most industrial applications need about 100 PSI, which both rotary screws and reciprocating compressors can easily provide. For pressures above 120 PSI, a multi-stage compressor may be necessary.
Rotary screw compressors with a single-stage design are capable of delivering up to 150 PSI while the two-stage ones generally provide over 175 PSI. These compressors excel in delivering higher CFM with greater efficiency rather than achieving extreme pressures.
In contrast, single-stage reciprocating compressors can compress air to 120 PSI, and its two-stage models can similarly reach north of 175 PSI. For speciality applications requiring very high pressures—up to 6,000 PSI or more—multi-stage piston compressors with three or four stages are the preferred choice. These are often used in specialty applications.
2. Pressure Bands
Pressure bands reflect a compressor’s ability to maintain consistent pressure (PSI) levels within a system, defined by the difference between the cut-in and cut-out pressures.
Rotary screw compressors typically operate within narrower pressure bands and thus excel at generating stable output, with variable speed drive (VSD) models being the most precise, maintaining a tolerance of +/- 1.5 PSIG. This precision allows for reducing overall plant pressure without falling below minimum requirements. Fixed-speed rotary compressors also provide tighter bands than piston compressors due to their ability to produce air continuously.
On the other hand, since reciprocating compressors produce air intermittently and often have duty cycles below 100%, their pressure bands are wider—ranging from +/- 10 to 30 PSIG. To maintain stable delivery pressure, a properly sized storage tank is crucial.
3. Energy Efficiency
The energy efficiency of reciprocating and rotary screw compressors ultimately depends on the application. Reciprocating compressors are slightly more efficient at lower CFM and horsepower ratings, particularly in intermittent usage scenarios. However, rotary screw compressors excel in high-CFM and continuous-use applications, delivering greater CFM per horsepower.
- Rotary Screw Compressors:- Fewer moving parts reduce friction and energy loss.
- Produce air continuously during operation, maximising efficiency.
- Experience minimal internal leakage due to their design, enhancing performance.
- Generate air only during half of each cycle.
- Lose more energy to friction and motion of internal parts.
- Internal leakage from piston motion and component wear reduces overall efficiency.
4. Duty Cycle
The duty cycle reflects how much time a compressor spends producing air versus resting. This is a key differentiator between reciprocating and rotary screw compressors.
Rotary screw compressors are designed for 100% duty cycle (continuous operation) and can therefore produce air without interruption, save for short unloading periods when less air is needed. This makes them Ideal for applications demanding a continuous-run compressor.
Meanwhile, reciprocating compressors can only operate at intermittent duty cycles, with cooling periods required between operations. As a refresher, duty cycle ratings (e.g., 25%, 50%, 75%, or 100%) indicate how much time the compressor can spend producing air before resting, and most piston compressors have a duty cycle of 20–30%. Overuse can cause overheating and reduce lifespan.
5. Cleanliness of Air Output
Both piston and rotary screw compressors can deliver clean air with proper filtration and treatment, but rotary screw compressors have a distinct advantage in maintaining air cleanliness.
- Rotary Screw Compressors- Deliver cleaner air with minimal particulate contamination and oil carryover due to their enclosed design.
- Less susceptible to oil leakage, with many models featuring built-in filtration systems for removing contaminants from the oil.
- Ideal for applications requiring consistent air purity.
- More exposed to the environment, allowing dust, dirt, and other contaminants to enter the compressed air.
- Higher likelihood of oil leakage, increasing the risk of air supply contamination.
Conclusion
The right air compressor for you ultimately depends on your specific needs. Reciprocating compressors are versatile, easier to maintain, and well-suited for intermittent-use applications. In contrast, rotary screw compressors deliver higher output and excel in large-scale industrial settings requiring continuous airflow. By evaluating your application’s requirements—such as usage patterns, pressure needs, and air quality—you can confidently choose the compressor that best meets your expectations.