Industrial Pump Upkeep: Why Predictive Monitoring Matters
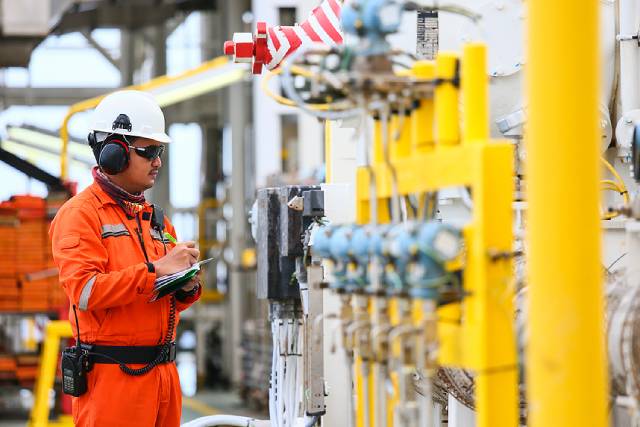
Pump failure is not something that happens suddenly. In fact, malfunctioning pumps in Singapore give off many warning signs long before breaking down. A pump in distress may continue working for a while, but neglecting its warning signs is a risk waiting to unfold. As such, it is important to recognise these indicators to avoid a costly disaster in the near future. This is where predictive pump monitoring comes in to facilitate a timely intervention. Read on as we go into further detail about this concept and why implementing it guarantees a much smoother daily workflow.
Understanding Predictive Pump Monitoring
Pump condition monitoring is a core part of a predictive maintenance strategy, and it leverages advanced technology to monitor and manage pump systems in real-time. Through the use of sensors and digital tools, operators can track essential performance data—such as temperature changes, vibration patterns, and electronic signatures—to gain real-time insights into the health of their equipment.
Using AI-driven software, key data from these sensors is catalogued and analysed instantly, allowing operators to catch anomalies early and address potential issues before they worsen. This not only minimises the risk of disastrous breakdowns but also extends the lifespan of the pumping equipment, reduces downtime, and enhances overall productivity.
The Main Benefits of Predictive Monitoring
1. Proactive repairs and maintenance scheduling
Predictive monitoring helps detect irregularities or signs of wear early, allowing operators to address maintenance needs proactively. By identifying potential issues in components like seals, bearings, and valves before they escalate, this approach minimises unexpected shutdowns and costly repairs. Knowing when a part is likely to fail enables more precise maintenance planning, so you can replace components only as needed rather than relying on fixed schedules that may result in premature servicing or delayed repairs.
For example, if a mechanical seal starts showing signs of pressure loss, predictive monitoring can send an alert notification about it immediately, allowing operators to make the necessary fixes before it impacts the system. This targeted maintenance approach saves on time and expenses and does much to extend equipment life.
2. Real-time monitoring and data analysis
Instantaneous data collection and analysis is an incredibly powerful tool for those who can take advantage of the information it provides. With real-time data, one can proactively monitor and continuously track crucial performance indicators, including motor efficiency, flow rate, pump pressure, temperature, and vibration levels.
This level of detail allows operators to always stay on top of each component’s condition and anticipate issues before they interrupt operations. Instant data analysis also provides insight into overall system health, helping to identify performance trends and possible inefficiencies.
3. Pump optimisation
A combination of predictive monitoring and proactive maintenance does wonders in extending any industrial pump’s lifespan and optimising its performance. By constantly collecting and analysing data while the pump is in operation, operators gain a bird’s eye view of the system’s current efficiency, including key metrics like energy usage. This data enables precise adjustments and supports decisions on configuration upgrades to improve performance over time.
For even greater efficiency, predictive monitoring can be integrated with automated control systems and specialised equipment, such as variable frequency drive (VFD) motors. With data-driven insights, the system can automatically adjust its settings to maintain optimal performance, balancing energy use and output based on current demands. This adaptive capability not only maximises efficiency but also enhances reliability, as the technology constantly learns from collected data to fine-tune operations.
In this way, predictive monitoring becomes a valuable tool for maintaining peak performance and ensuring that your pump system operates smoothly and cost-effectively on an ongoing basis.
Conclusion
Incorporating predictive maintenance through condition monitoring for industrial pumps is a transformative approach that maximises uptime and operational efficiency. As we've discussed, predictive maintenance is much more than a buzzword—it's a proven strategy that uses advanced sensors and analytics to help organisations anticipate and address potential pump issues before they escalate into costly failures. By adopting this proactive approach, companies can reduce unplanned downtime, optimise maintenance schedules, and protect their equipment investment, ultimately ensuring a smoother, more reliable workflow.