Vacuum Pumps And Their Role In The Chemical Industry
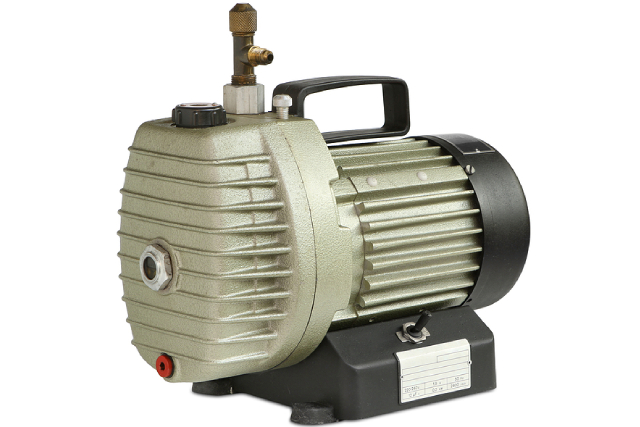
Vacuum pumps are essential components in the chemical industry, playing a critical role in a variety of processes. These devices are designed to create a vacuum by removing gas molecules from a sealed volume, creating a pressure differential that enables various chemical processes to occur more efficiently and safely. The importance of vacuum pumps in the chemical industry cannot be overstated, as they contribute to the production of a wide range of products, from pharmaceuticals to petrochemicals, by facilitating processes such as distillation, drying, and degassing.
Types of vacuum pumps
There are several types of vacuum pumps used in the chemical industry, each with unique characteristics and applications:
1. Rotary vane pumps: These are the most commonly used vacuum pumps in the chemical industry. They consist of a rotor with vanes that slide in and out, creating a vacuum as the rotor turns. Rotary vane pumps are known for their reliability and efficiency in creating low to medium vacuums, making them suitable for various chemical processes.
2. Diaphragm pumps: These pumps use a flexible diaphragm to create a vacuum. They are often used for applications that require a clean, oil-free vacuum, such as handling aggressive chemicals or corrosive gases. Diaphragm pumps are ideal for processes where contamination must be avoided.
3. Screw pumps: Screw pumps, also known as dry screw vacuum pumps, use two intermeshing screws to compress gas and create a vacuum. They are highly efficient and capable of handling large volumes of gas, making them suitable for demanding applications in the chemical industry. Screw pumps are also known for their ability to handle condensable vapours and particulate-laden gases without contamination, thus maintaining process purity.
4. Liquid ring pumps: These pumps use a liquid, usually water, to create a vacuum. They are robust and can handle wet and corrosive gases, making them ideal for chemical processes that involve significant moisture or solvents. Liquid ring pumps are often used in vacuum distillation and solvent recovery processes.
5. Diffusion pumps: These pumps use a high-speed jet of vapour to direct gas molecules towards the pump outlet. They are capable of achieving very high vacuums and are often used in combination with other pumps to achieve ultra-high vacuums required for specific chemical processes.
Applications of vacuum pumps in the chemical industry
1. Distillation: Vacuum distillation is a process that separates components in a mixture based on differences in boiling points. By reducing the pressure, vacuum pumps lower the boiling points of the substances, allowing distillation to occur at lower temperatures. This is particularly important for heat-sensitive materials that might decompose at higher temperatures.2. Drying: Vacuum drying removes moisture from materials, which is crucial in the production of powders and granules. By using vacuum pumps, the drying process is more efficient and can be performed at lower temperatures, preserving the quality and integrity of the product.
3. Degassing: Vacuum pumps are used to remove dissolved gases from liquids, which is essential in producing high-purity chemicals and materials. Degassing prevents defects and impurities in the final product, ensuring consistency and quality.
4. Filtration: In the filtration process, vacuum pumps are used to create a pressure differential that drives the filtration of liquids through a filter medium. This accelerates the filtration process and improves the efficiency of separating solids from liquids.
5. Centrifugation: Vacuum pumps are used in centrifugation processes to enhance the separation of components based on density. By creating a vacuum, the efficiency of the centrifugation process is improved, leading to faster and more effective separation.
6. Chemical synthesis: Many chemical synthesis processes require a controlled environment with low pressure to proceed efficiently. Vacuum pumps help create and maintain these conditions, enabling precise control over reaction parameters and improving yield and purity.
Benefits of using vacuum pumps
The use of vacuum pumps in the chemical industry offers several benefits:
1. Energy efficiency: Modern vacuum pumps are designed to be energy-efficient, reducing the overall energy consumption of chemical processes. This is particularly important in large-scale operations where energy costs can be significant.2. Process safety: Vacuum pumps enhance process safety by reducing the risk of explosions and fires in processes involving volatile substances. Lower operating pressures reduce the likelihood of hazardous reactions.
3. Product quality: By enabling processes to occur at lower temperatures and preventing contamination, vacuum pumps help maintain the quality and purity of the final product. This is crucial in industries like pharmaceuticals, where product quality is paramount.
4. Environmental impact: Vacuum pumps can reduce the environmental impact of chemical processes by minimising the release of harmful gases and vapours. This contributes to a cleaner and safer working environment.
Conclusion
Vacuum pumps play a pivotal role in the chemical industry, enabling efficient and safe chemical processes. From distillation and drying to degassing and chemical synthesis, these pumps are indispensable in producing high-quality chemicals and materials. For companies seeking to optimise their operations and improve energy efficiency, conducting an energy audit in Singapore can provide valuable insights.
At Winston Engineering, we offer a range of high-performance vacuum pumps, including screw pumps, tailored to meet the specific needs of the chemical industry. Our expertise ensures that you get the best solutions for your applications, enhancing productivity and sustainability.