Welcome to WINSTON ENGINEERING SINGAPORE! You can choose another country below to see content specific to your location and shop online.
Turbo Blowers and Compressors
(The above illustration shows the primary internal components of Turbowin Core, including the PM Motor, Air Foil Bearing and Impeller.)
Discover unparalleled efficiency and reliability with our turbo blowers and compressors. Engineered for optimal performance, cutting-edge technology, reduced environmental impact, and superior functionality. Explore a wide range of solutions tailored to meet diverse industrial needs.
Turbo Blowers
A turbo blower is a type of blower used for aeration in various applications, such as wastewater treatment plants. It's designed to provide a continuous supply of air or oxygen to support biological processes. Turbo blowers for wastewater in Singapore are often characterised by high-speed operations, energy efficiency, and compact design. They may use technologies like magnetic bearings and direct drive systems to achieve these characteristics. The primary purpose of turbo blowers for wastewater is to provide a reliable and efficient source of air for aeration in processes like activated sludge treatment.
Turbo Compressors
A turbo compressor is a device that compresses air or other gases. It's a general term that can encompass various types of compressors, including centrifugal compressors and axial compressors.
In the context of industrial processes, turbo compressors in Singapore are often centrifugal compressors. These machines use a rotating impeller to accelerate air, and then a diffuser slows down and redirects the air, causing compression. Commonly used in applications such as natural gas processing, refrigeration, and industrial air compression.
In the context of industrial processes, turbo compressors in Singapore are often centrifugal compressors. These machines use a rotating impeller to accelerate air, and then a diffuser slows down and redirects the air, causing compression. Commonly used in applications such as natural gas processing, refrigeration, and industrial air compression.
Compressed Air Quality
Compressed air quality is crucial for many applications, especially in industries such as manufacturing, pharmaceuticals, electronics, and food processing. The quality of compressed air is typically defined by factors such as moisture content, oil content, particulate matter, and microbial contamination.
Turbo compressors and screw compressors are both types of positive displacement compressors used in various industrial applications. They have distinct characteristics, and their suitability depends on specific requirements. Let's compare the air quality aspects of turbo compressors and screw compressors:
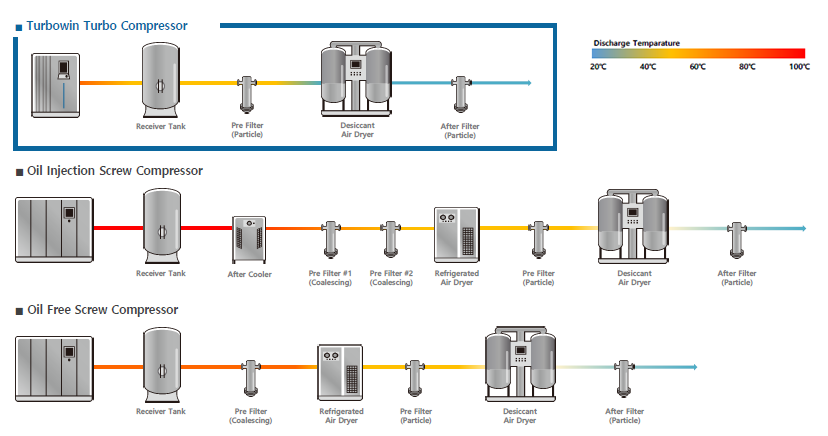
(The above illustration shows the comparison of TurboWin compressed air quality with screw compressor.)
1. Oil-Free Operation:
Turbo Compressors: Generally, turbo compressors offer oil-free operation. Turbo compressors use magnetic or airfoil bearings, eliminating the need for lubrication systems that can introduce oil into the compressed air stream.
Screw Compressors: While some screw compressors can provide oil-free air, others require lubrication for their operation. Special designs, such as oil-injected and oil-free screw compressors, are available.
Turbo Compressors: Generally, turbo compressors offer oil-free operation. Turbo compressors use magnetic or airfoil bearings, eliminating the need for lubrication systems that can introduce oil into the compressed air stream.
Screw Compressors: While some screw compressors can provide oil-free air, others require lubrication for their operation. Special designs, such as oil-injected and oil-free screw compressors, are available.
2. Air Contamination:
Turbo Compressors: They are often preferred in applications requiring high-quality, oil-free compressed air. The absence of lubrication systems minimises the risk of oil contamination.
Screw Compressors: Oil-injected screw compressors may introduce oil into the compressed air. Oil-free screw compressors are designed to eliminate this risk, making them suitable for applications demanding high air quality.
3. Compressed Air Purity Standards:
Turbo Compressors: Commonly used in applications where adherence to strict compressed air purity standards, such as ISO 8573-1, is crucial.
Screw Compressors: Depending on the design (oil-injected or oil-free), screw compressors can meet various purity standards. Oil-free screw compressors are designed for applications demanding the highest air quality.
4. Maintenance and Contamination Risks:
Turbo Compressors: Generally have fewer components and lower maintenance requirements, reducing the risk of contamination from oil or other contaminants.
Screw Compressors: Oil-injected screw compressors require regular maintenance to ensure proper lubrication and prevent oil contamination. Oil-free screw compressors typically have higher initial costs but offer lower maintenance requirements.
5. Energy Efficiency:
Turbo Compressors: Often more energy-efficient at full load compared to screw compressors. However, their efficiency might drop at partial loads. TurboWin compressor build with smart and compact design due to its Permanent Magnet motor's efficiency.
Screw Compressors: Can be more energy-efficient at partial loads, making them suitable for applications with varying air demand.
Return-of-Investment (ROI) TurboWin Compressor:
1. Fewer Moving Parts:
Turbo compressors typically have fewer moving parts compared to screw compressors. This can result in simpler maintenance requirements and potentially fewer points of failure. TurboWin guaranteed 100% oil free as compare to those conventional oil free type of compressors. It able to prevent contamination and prolong life span to entire air system, as well as secured production quality.
2. No Lubrication System:
Many turbo compressors operate without a lubrication system, as they use magnetic or airfoil bearings. This eliminates the need for oil changes and reduces the risk of oil-related maintenance issues.
3. Lower Maintenance Frequency:
Due to their design, turbo compressors often require less frequent maintenance compared to screw compressors. This can lead to reduced downtime and operational disruptions. Total maintenance free due to the zero friction air bearing with the existence of NASA technology.
4. Advanced Monitoring Systems:
Turbo compressors often come equipped with advanced monitoring systems that provide real-time data on the compressor's performance. This allows for proactive maintenance and troubleshooting, minimising the chances of unexpected breakdowns.
5. Higher Reliability:
The simplicity of turbo compressor design and the absence of certain components, such as oil-lubricated bearings, contribute to higher reliability and reduced maintenance hassles.
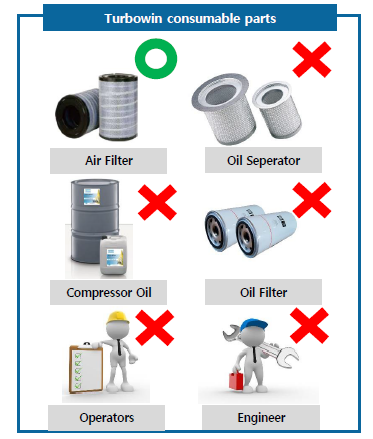
Turbo Compressor vs Screw Compressor
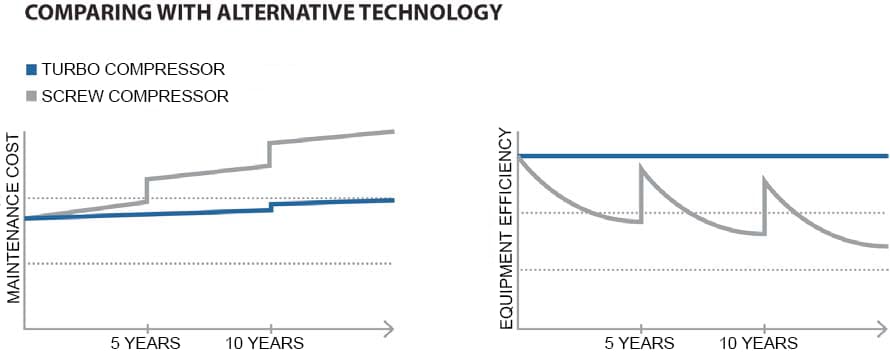